スマートファクトリーで何が変わる?現在の課題とロードマップをわかりやすく解説
2023/11/20
ODM基板開発
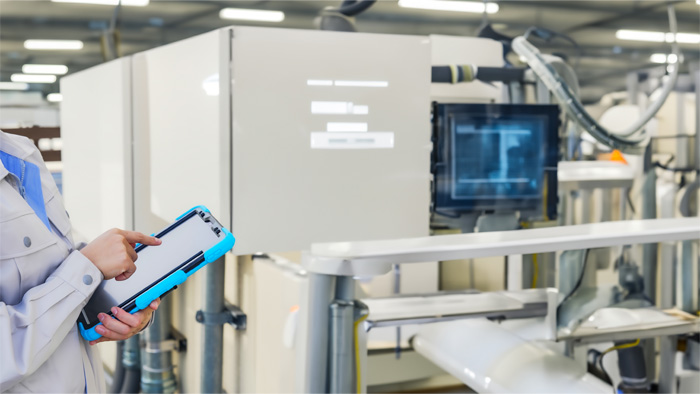
近年、IoTやAI、ビッグデータなどを活用した「ものづくりのスマート化」への取り組みが重要となってきています。これに関連して、「スマートファクトリー」という言葉を耳にするようになりました。スマートファクトリーとは、どのような工場なのでしょうか。
今回は、スマートファクトリーでどんなことができるのか、メリットと課題、ロードマップを中心にわかりやすく解説していきます。
スマートファクトリーとは?
スマートファクトリー(スマート工場)には、学問的な定義はありません。スマートファクトリーとは、一般にIoTやAI、ビッグデータ処理などの先進技術を駆使することにより、デジタルデータを基に業務を管理する工場をいいます。スマートファクトリーが実現すれば、業務プロセスを改善したり、高品質の製品を低コスト・短期間で生産したり、工場の生産性を継続的に向上させたりすることができます。
スマートファクトリーは、従来の製造業におけるロボットなどの機械を活用した自動化とは違い、データの収集と活用が軸になっています。データの収集と活用により業務プロセス全体を見直せる点と、的確な業務フローを自動的に分析し生産現場で活用することで業務効率化を実現できる点がスマートファクトリーの大きな特徴です。
スマートファクトリーの市場規模
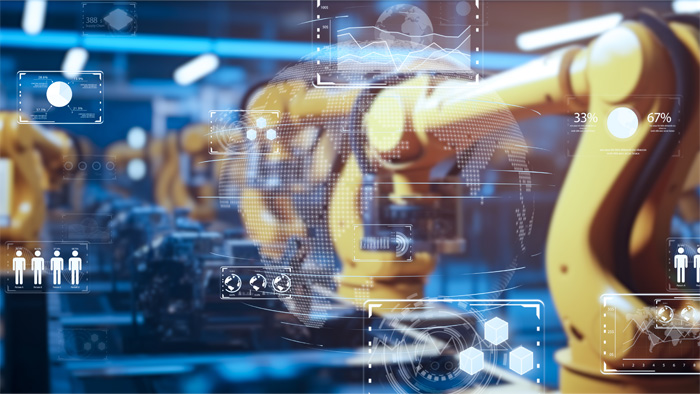
スマートファクトリーの概念は、元々ドイツ政府が主導する国家プロジェクト「インダストリー4.0(Industry 4.0)」に端を発しています。海外では、「インダストリー4.0」のほかに、米国の民間企業が主導する「インダストリアル・インターネット・コンソーシアム(Industrial Internet Consortium:IIC)」などの「第4次産業革命」と呼ばれる変革の波により、工場管理が大きく変わろうとしています。
日本でも、AIやIoTを活用することにより、労働力人口の減少時代における効率的なものづくりを目指しています。スマートファクトリーをスムーズに進めるために、経済産業省は「スマートファクトリーロードマップ 〜第4次産業革命に対応したものづくりの実現に向けて〜」を公開しています。
米国の市場調査会社であるGrand View Research社の調査によれば、世界のスマートファクトリー市場規模は、2030年には2719億1000万ドル(約40兆円)に達する見込みとのことです。
スマートファクトリーのメリットと課題
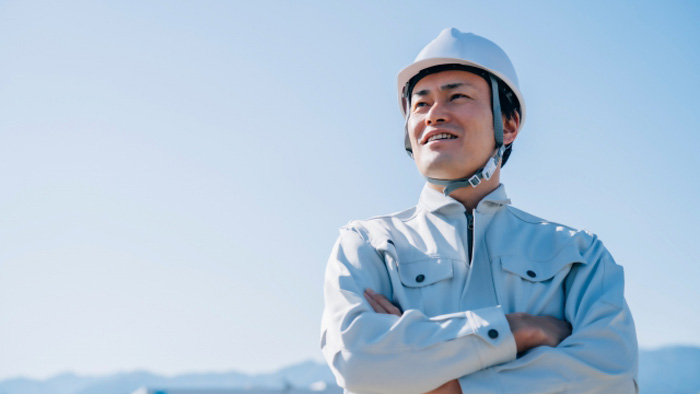
スマートファクトリーのメリットと課題は以下の通りです。
スマートファクトリーのメリット
メリット1:現場の状況の可視化
センサー、簡易端末、カメラなどを活用して国内外の工場を遠隔監視することで、どこで何が起きているのか、稼働状況や問題発生をリアルタイムに可視化(見える化)できます。現場の状況が可視化されることで、稼働状況に応じて柔軟な対応が可能です。これによって、品質が高く低コストの製品の製造が期待できます。
メリット2:現場の省人化・適切な安全対策
ロボットや自動判別システムの導入により、生産現場の自動化が可能です。また、過去の設計事例をデータベース化して、シミュレーションソフトで解析することで、製品の設計も自動化できます。生産現場と設計部門とがデータ活用を連携すれば、設計業務および生産業務の最適化が可能です。さらに、現場作業員の状況をタイムリーに把握することで、安全な職場環境が実現できます。
メリット3:技能の継承
AI技術を駆使した現場のデジタル化により、熟練技術者の技能やノウハウがデータ化されます。その結果、体系化した技能やノウハウを各生産拠点で共有したり、AIが組み込まれたロボットに学習させたりすることができるため、技能の継承も推進されます。
スマートファクトリーの課題
課題①デジタル化の浸透が遅れている
製造業は、他の業界と比べてデジタル化があまり進んでいません。IT技術に関するリテラシー不足、デジタル化に対する現場の抵抗やITが生産技術の重要な一部であるという認識の欠如などが課題となっています。ITに関してある程度の知識があれば、スマートファクトリーを実現するためのシステム、デバイスや機材を導入する場合に適正な判断が可能になります。
課題②経営効果を追求する取り組みが失われている
生産現場では、個別課題を解決する取り組みは多いもののAIやIoTに代表される技術を工場経営の改善に役立てるという意識が希薄です。工場経営の改善は、さまざまな要素を考慮して工場全体を広い視野で捉え、どの工程のどの課題の解決に取り組むのが最も効果的かを考えて実践する必要があります。その際、現場の部門ごとのスペシャリストはもちろん、流通・販売に詳しい人材やデジタル人材を含む、あらゆる関係者との連携や協力が大切になります。
スマートファクトリー実現に向けたロードマップ
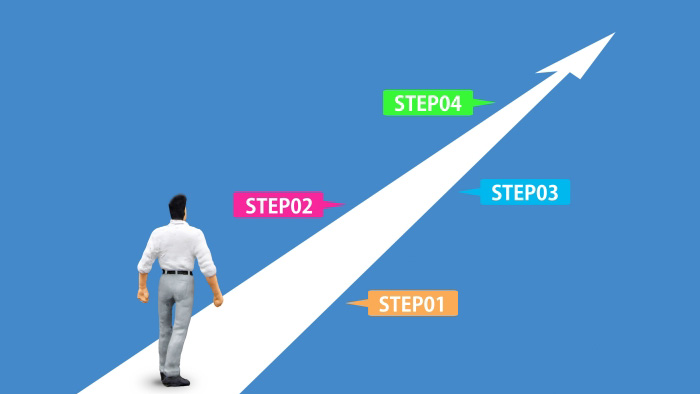
「スマートファクトリーに関心はあるが、何から始めればよいのかわからない」工場関係者の方から、そういった声を聞くことがあります。そこで、既存の工場にスマートファクトリーを導入する場合に、どれから着手すればよいのか、現場の現状の課題ごとにスマートファクトリー実現に向けたロードマップの例を以下に示します。
【現場の課題1:個別原価を把握できない、納期遅延が頻発】
→デジタル化(Digital transformation:DX)から着手
どのオーダーのどの部品が、どの工程でどこまで処理が進んでいて、いつ出荷できるのか、といったデータを自動的に取得することにより納期を順守可能な生産スケジュールおよび作業手順の管理を徹底させる必要があります。また、状況に応じて、製造実行システム(Manufacturing Execution System:MES)の導入が必要な場合もあります。
【現場の課題2:人手不足、品質のばらつき発生】
→ロボット化・自動化(Robotics transformation:RX)から着手
ロボット化・自動化(RX)が目指すのは、特に単調できつい労働の解消です。こうした作業は、本来人間がやるべきものではなく、現場の人手不足の元凶となります。現場の人手不足や高い離職率のほかに、手作業に起因する品質のばらつきの発生が、人手不足から起因する場合には、ロボット化・自動化を優先させるとよいでしょう。ただし、ケースによっては工場のレイアウトを変更したり、建屋を改修したりすることがある点も留意しておきたいところです。
【現場の課題3:省エネ、CO2排出量削減】
→グリーン化(Green transformation:GX)から着手
近年、国が掲げる、2030年のCO2排出量削減目標に準じて、どのように工場の脱炭素化を進めていくかが企業の新しい課題となっています。脱炭素化は、地球環境の保護とともに省エネにもつながります。工場内の動力、加熱、空調、照明などに必要なエネルギーを需要する側と、クリーン電力の調達、自家発電、熱電供給、エネルギー管理システムなどのエネルギーを供給する側の双方からの取り組みが必要です。
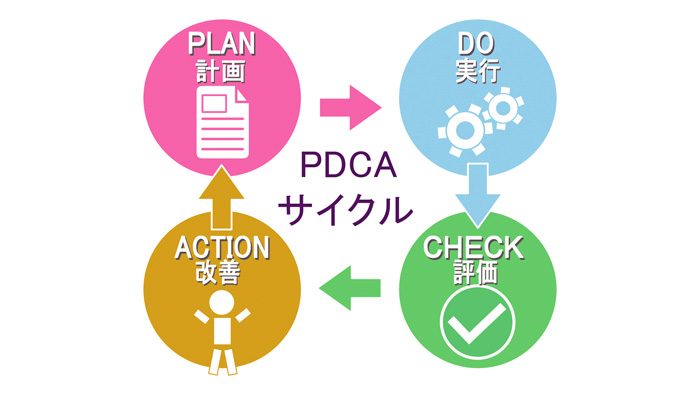
このようなロードマップを成功させるためには、最初は小さく始め、短いステップでPDCA[Plan-Do-Check-Act (Action)]サイクルを回して、システムおよび運用の検証や改善を図りながら進めていくことが重要です。
経済産業省の「スマートファクトリーロードマップ」に掲載されている各企業の先行事例では、課題に対するソリューション(解決策)などがイメージ図とともに、分かりやすくまとめられているため参考になります。
スマートファクトリーの導入は、目的ではなく手段です。その主なねらいは、優秀な人材を引き付け新しい生産の方式を生み出して高収益と成長につなげることにあります。企業がスマートファクトリー導入をスムーズに進めるには、既存工場の現状の課題を把握することが重要です。課題が明確であれば、それを解決するために実行すべきアクションを絞ることができます。